(almost) Complete
This is what I've got since last time. A circuit board that included every component from this list here: Radioshack Wish List (except for the optional PC board terminals and the Coil making materials - for instructions on how I made my coils with the material on hand, view earlier posts).
I also created a volume attenuator following these directions, because I did not particularly desire to use an optical solar-cell volume control. Finally, I constructed the antenna circuit using these directions, and procured an antenna from an old CD boombox.
Here are some pictures of my components:
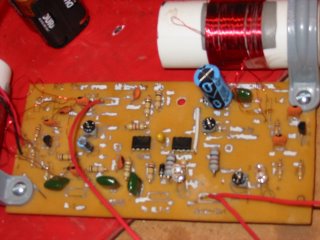
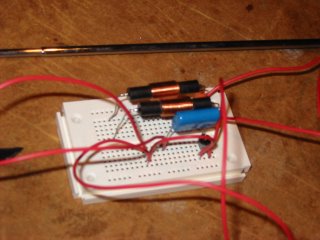
(both volume and antenna circuits on the one board)
Now, my current problem is that I do not get any audio out of the Audio Out on my Theremin board. I have tried putting a 1/4 inch input jack through the volume Audio Out, and even a direct connection to the Audio Out. Not sure what could be the problem here, will have to do some more troubleshooting over weekend.
On a happier note, I did tune the coils to the AM Radio, and I will try and get the video of the coil testing up. It has some neat theremin-esque noises eminating from this project.